Continuous Casting Rolls
Manufacturing the full supply chain from alloy design to manufacturing and developing a wide range of flux cored welding wires suitable for submerged arc welding and open arc welding of continuous casting rolls to implementing welding procedures, automatic weld-overlay cladding, machining and post weld heat treatment of rolls enable Aliaj Joosh to be able to provide a complete package to OEMs, end users and customers.
Specific solutions from introducing super austenitic stainless steel material designed for foot rolls and top zone rolls which displays outstanding performance compared to conventional martensitic stainless steels and customised precipitation hardened martensitic stainless steel designed for the bender and straightening sections are the best practice of our dedication to our customers commitment.
Our advanced and improved flux cored welding wires and roll refurbishment solutions offer;
- High temperature oxidation and corrosion resistance
- Microstructurally stable at high temperatures
- Good weldability
- Maximum tempering resistance
- Reduced maintenance cost
- Good metal-to-metal wear resistance
Our capability is not limited to only welding and metallurgy and surface engineering. However, Aliaj Joosh team has a well capable and trained dedicated engineers and technicians to supply complete maintenance service package to continuous casting segments together with total package of segment installations.
The contact between the continuous casting roll surfaces and the slab is very complicated as few failure mechanisms tend to operate at the same time. The rolls often show premature corrosion marks according to inadequate welding materials or improper welding techniques. Rolls lifetime can also be less than satisfactory if the roll surfaces wear out and the required roll gap is no longer maintained. Aliaj Joosh delivers improved service life of the continuous casting rolls by:
- Understanding the continuous casting service conditions
- Determining the failure mechanisms
- Selecting the most suitable alloys
- Establishing welding procedures to weld-overlay the rolls and achieve the most desirable microstructure
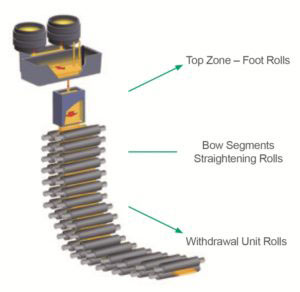
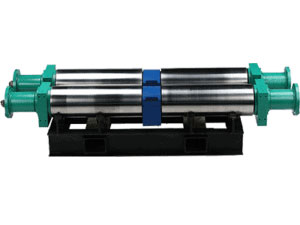
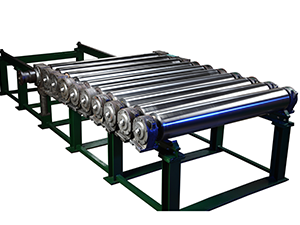
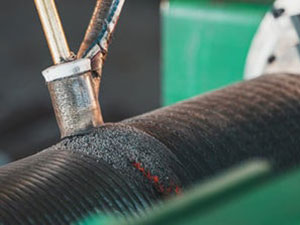
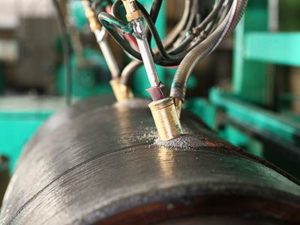
Hot Strip Mill Rolls
Hot Strip Mill process is reducing the thickness of continuously cast steel thickness via a number of rolls. Aliaj Joosh has the expertise and experience of refurbishing various rolls installed in hot rolling mills:
- Table rolls
- Transportation rolls
- Scale breaker rolls
- Edger rolls
- Roughing rolls
- Pinch rolls
- Wrapper rolls
- ROT rolls
Our capability in refurbishing rolls is not only limited to flat products but also enhanced in shaped steel products as well.
due to loading stresses, metal-to-metal wear mechanism, high corrosion environment in HSM plant and more importantly significance of the rolls surface quality, roll refurbishing process is very challenging and demanding.
Aliaj Joosh team of engineers has extensive knowledge and experience to understand the application and accordingly able to select the best cladding alloys from various tools steels, specific martensitic stainless steels, super austenitic stainless steel and Cobalt and Nickel based alloys to overcome these issues on different rolls to minimise:
- Surface cracks
- Metal-to-metal wear
- High temperature oxidation
- Corrosion
- Thermal and mechanical fatigue stresses
- Pick up characteristic
And to maximise:
- Lifetime
- Availability
- Durability
- Performance
- Surface quality
And in result enhancing the quality of the finish products in HSM plants.
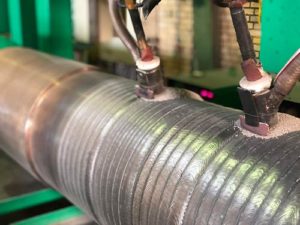
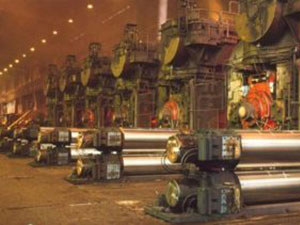
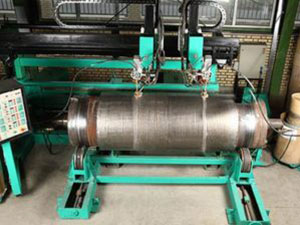
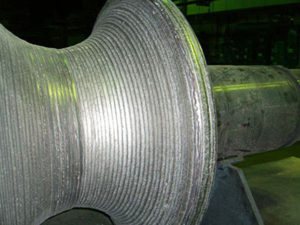
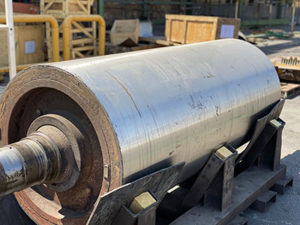
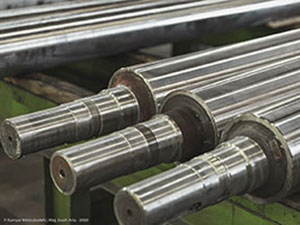